PRÉPARATION DE PÂTE
PULPAGE ET RAFFINAGE
Le pulpage et le raffinage sont les deux premiers traitements que subit la pâte dans le processus papetier. Ils sont essentiels à l’obtention de caractéristiques de fibres adaptées à la qualité du produit fibreux final et à la bonne machinabilité de la feuille sur la ligne de production. La grande expertise d’Allimand dans ces domaines est la garantie d’une conception de ligne réunissant toute l’expérience acquise au travers de ses nombreux projets pour des papiers à haute valeur ajoutée.
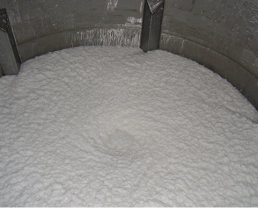
PULPAGE ET RAFFINAGE
PULPEUR
Le premier élément constitutif d’une ligne de production de papier est le pulpeur qui sert à mettre des balles de pâte en suspension. La qualité de mise en suspension est très importante pour l’efficacité des traitements ultérieurs de la pâte.Nos pulpeurs pour pâtes vierges et vieux papiers propres sont constitués :
- d’une cuve de construction mécano-soudée en acier inoxydable
- d’un rotor à géométrie étudiée
- d’une grille perforée monobloc en inox
- d’un entraînement par moteur horizontal et réducteur ou par moteur vertical et courroies.
Leur fonctionnement en mode continu ou discontinu peut s’effectuer par commande manuelle ou en mode automatique.
L’optimisation de la séquence de pulpage se fait par ajustement des paramètres de pulpage : température, concentration de travail, temps de pulpage, choix d’additifs et géométrie de la grille perforée. A chaque type de pâte et de papier ses conditions optimales de fonctionnement. Les avantages des pulpeurs Allimand sont la robustesse de construction, les économies d’énergie et la maintenance aisée.
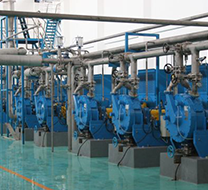
PULPAGE ET RAFFINAGE
RAFFINEUR
Le raffinage est le traitement clé de la pâte. Allimand a des compétences essentielles quant aux conditions opérationnelles qui définissent les caractéristiques finales des fibres : longueur de coupe, degré de raffinage et niveau de fibrillation. Les qualités du papier en sont directement impactées : allongement, résistance à la rupture, déchirure, opacité, porosité, double pli… Les raffineurs Double disque ALLIMAND existent en plusieurs tailles (20″, 28″ et 36″). Ces raffineurs sont de type Duoflo avec deux entrées de pâte permettent un meilleur équilibrage et une meilleure stabilité de raffinage. Ces raffineurs sont utilisés pour tout type d’application et notamment pour les papiers de spécialité à haut degré de raffinage.
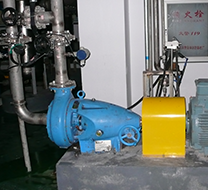
PULPAGE ET RAFFINAGE
DÉPASTILLEUR
Le dépastillage est un traitement essentiel soit pour désintégrer les agglomérats de pâte, soit pour assurer une bonne homogénéité de pâte avant raffinage ou classage. Les savoir-faire process et opérationnel d’Allimand assurent une fenêtre de fonctionnement optimale pour cet équipement. Allimand fabrique ses propres dépastilleurs particulièrement adaptés aux fibres vierges et aux cassés, notamment pour les papiers difficiles comme les résistants à l’état humide.Les éléments constitutifs du dépastilleur sont :
- Des garnitures de Rotor et Stator en acier inoxydable à résilience spéciale et résistantes à l’abrasion
- Un réglage manuel par volant avec positionnement automatique des garnitures
- Des sécurités mécaniques et électriques
- Des presse-étoupes sec ou à anneau d’eau
PRÉPARATION DE PÂTE
MÉLANGE
Les stabilités de la marche machine et de la qualité du produit fibreux final sont la résultante de règles hydrauliques et de conception rigoureuses dont l’une des étapes clés est le mélange des divers constituants de la pâte. L’expertise d’Allimand excelle dans le mélange homogène des différents types de pâte (fibres longues et fibres courtes), des divers additifs et des charges. Les conséquences process directes sont une rétention de fibres et de charges constante et une pré-disposition naturelle à une formation de qualité.
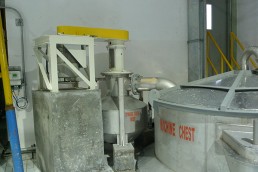
MÉLANGE
MÉLANGEUR DYNAMIQUE
L’homogénéité du mélange des pâtes est essentielle pour assurer la marche stable de la machine à papier et la régularité en sens marche et travers des caractéristiques du papier.
Allimand a développé un mélangeur dynamique révolutionnaire qui a tout d’abord été installé sur des lignes de production de papier de spécialité pour ensuite être étendu à toutes sortes de papier.
Les divers flux de pâte sont injectés de telle sorte que la simple injection permette déjà un bon mélange. Une plaque perforée et un agitateur finissent de mélanger de manière constante et rapide les différents flux.
Cette technologie permet de ne plus avoir de cuvier de mélange, diminue le temps de rétention et permet dans le cas de papiers colorés d’avoir des changements de sortes plus rapides.
PRÉPARATION DE PÂTE
CIRCUIT COURT
Le circuit court constitue la dernière phase de traitement de la pâte avant son envoi sur la machine à papier. Allimand a toujours été un leader sur la conception de cette étape, notamment au niveau de la régularité de fonctionnement (contrôle de dilution de pâte et automation des boucles) et de l’efficience de décontamination de la pâte. Ceci garantit une alimentation optimale et homogène de la pâte sur machine.
CIRCUIT COURT
ÉPURATION CYCLONIQUE
La propreté de la pâte envoyée sur machine est un impératif pour obtenir un papier sans défauts tels que présence d’amas fibreux, de points noirs ou de trous. Allimand intègre sur ses circuits courts une épuration cyclonique dont la conception individuelle de chaque cleaner et le type d’étagement définissent un degré d’efficacité d’épuration et de limitation de pertes en fibres ou en charges. Elle assure l’élimination des contaminants légers et lourds ainsi que de l’air entrainé.
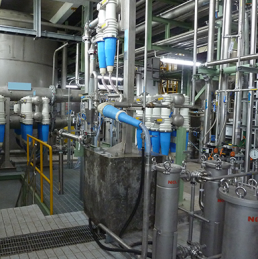
CIRCUIT COURT
ÉPURATION SOUS PRESSION
L’épuration sous pression par classage à paniers à fentes ou à trous est le dernier traitement apporté à la pâte avant son envoi sur la machine à papier. Son efficacité est essentielle pour assurer une propreté de pâte nécessaire à la fabrication de papiers sans contaminants qui peuvent être aussi à l’origine de casses papiers, facteur important de l’efficience machine.
Les tamis sont adaptés à la classe et aux caractéristiques des fibres (bois, synthétiques, naturelle). Le nombre d’étages est défini par les débits, les pertes en fibres résiduelles et le type de papiers ou voiles fibreux à produire.
Les connaissances profondes et étendues d’Allimand dans la conception de lignes d’épuration complexe et de production de papiers Hi-Tech sont l’assurance d’une parfaite adaptation des systèmes aux contraintes opérationnelles.
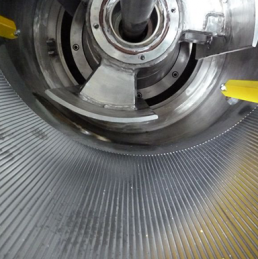
PRÉPARATION PÂTE
CIRCUIT DES CASSÉS
Le recyclage des cassés dans les circuits de préparation pâte est toujours une étape critique du process. Que ce soit pour les cassés humides ou les cassés secs, Allimand apporte un soin particulier à la sélection des équipements de traitement de pâte suivant les types de fibres, les sortes de papier et les traitements spécifiques apportés au papier sur la machine à papier.
Cette expertise Allimand, reconnue dans le monde entier, est aussi la garantie d’une homogénéité optimale de la pâte envoyée vers le circuit court.
CIRCUIT DES CASSÉS
PULPAGE
Le re-pulpage des cassés secs est une phase importante de pré-trituration. Elle assure une bonne remise en suspension des fibres et désagglomère les amas fibreux les plus gros. La température et le temps de pulpage associés à un ajout d’additifs spécifiques permettent d’alimenter les phases ultérieures de traitement des cassés avec la plus grande finesse et homogénéité de flux de pâte.
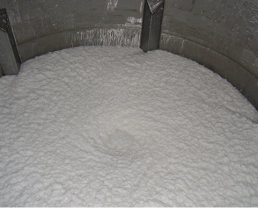
CIRCUIT DES CASSÉS
DÉPASTILLEUR
Le dépastillage des cassés secs remis en suspension est une séquence essentielle de trituration de la pâte. Il permet une séparation plus importante et plus fine des fibres par réduction du nombre d’agglomérats de papiers, notamment sur les papiers à résistance à l’état humide. La pâte dépastillée est ensuite envoyée vers un deuxième étage de classage avant réintroduction dans le système des cassés.
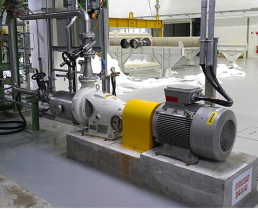
CIRCUIT DES CASSÉS
ÉPURATION SOUS PRESSION
Les fibres remises en suspension sont envoyées vers un épurateur sous pression à tamis pour séparer les fibres libres des fibres agglomérées. Elle permet aussi d’éliminer les contaminants qui peuvent avoir été introduits lors de la manipulation des cassés secs (cailloux, fils de fer…). Les contaminants sont alors envoyés vers un traitement secondaire de dépastillage.
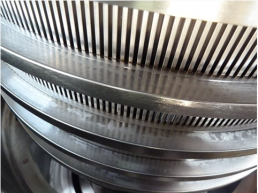
STOCK PREPARATION
CIRCUIT EAUX BLANCHES
Les contraintes environnementales imposées aux sites de production de papier (MES, DCO, consommation d’eau fraîche…) ont déterminé des règles de recirculation d’eaux process dans l’ensemble du procédé usine. Au niveau de la machine à papier, ce sont le traitement des eaux blanches et leurs réutilisations une fois clarifiées qui ont permis d’abaisser tous les ratios de consommation et de traitement des rejets.
Les connaissances et l’expertise d’Allimand ne se limitent pas au choix des procédés permettant de traiter de manière optimale ces eaux.
Ils concernent aussi l’adéquation du procédé aux conditions climatiques, aux contraintes propres à la sorte produite et aux limites de consommation en produits chimiques.
L’expérience d’Allimand sur le marché des papiers à haute valeur ajoutée permet d’assurer qu’à chaque sorte de matelas fibreux, un procédé sera choisi pour garantir une grande stabilité de fonctionnement de la machine à papier.
CIRCUIT DES EAUX BLANCHES
CLARIFICATION DES EAUX
Avant clarification, les eaux peuvent être pré-filtrées par une grille courbe permettant d’éliminer les poils de feutre des eaux issues de la section presses.
Ce recyclage de ces eaux est essentiel pour diminuer la consommation globale en eau fraiche de l’usine. Ce traitement simple et efficace permet aussi d’assurer un fonctionnement plus stable du système de clarification.
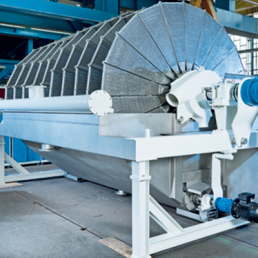
CIRCUIT DES EAUX BLANCHES
TRAITEMENT DES EAUX BLANCHES
Les eaux excédentaires des circuits des eaux blanches sont envoyées vers un traitement de clarification. Les trois principales méthodes utilisées dans l’industrie papetière sont la flottation, la décantation et la filtration.Le choix du procédé dépend de plusieurs paramètres :
-
- Type de fibres (bois, naturelles, synthétiques)
- Longueurs de fibres
- Taux de charges
- Physico-chimie des eaux
- Type de papiers
- Impératifs process spécifiquesLes compétences d’Allimand dans ce domaine qui touche directement la qualité des eaux process et leurs réutilisations est un facteur clé pour la production de papiers de qualité homogène et sans défaut.
Le choix affecte aussi la consommation globale en eau fraîche de l’usine et les valeurs de COD et de DBO des eaux rejetées.
Les contraintes environnementales de plus en plus pointues font de ce traitement une phase critique du processus global des rejets de l’usine.
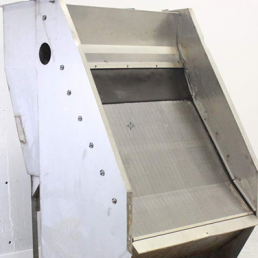