STOCK PREPARATION
PULPING AND REFINING
Pulping and refining are the two first pulp treatments in the papermaking process. They are essential to obtain the desired characteristics for the quality of the final fibre product. They are also essential for ensuring a good runnability of the sheet on the production line.
The design of Allimand machines is guaranteed by Allimand’s expertise in the areas of pulping and refining, its know-how and the experience gained through its new projects with high added value papers.
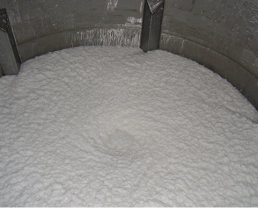
PULPING AND REFINING
PULPER
The first part in a paper production line is the pulper which suspends the raw stock bales. The quality of suspension is very important for the efficiency of the treatments applied later on to the stock.
Our pulpers for virgin pulp and clean waste paper are made up of:
- a tank made of mechanically welded stainless steel,
- a rotor, geometrically calculated,
- a stainless steel drilled screen block,
- a drive by horizontal motor and gear reducer or vertical motor and belts.
Their continuous or discontinuous operation modes can be manually or automatically controlled.
The pulping sequence can be optimized by adjusting the pulping parameters: temperature, working concentration, time of pulping, choice of additives and geometry of the drilled screen. Each type of pulp and paper has its optimum operating conditions. The main advantages of Allimand pulpers are that they are robust, save energy and have easy maintenance.
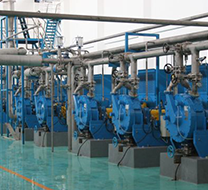
PULPING AND REFINING
REFINER
Refining is the key treatment of the pulp. Allimand has the skills required with regards to the operating conditions of refinement which define the final characteristics of the fibres: length of cut, degree of refinement and level of fibrillation. The paper qualities are directly impacted: stretching, breaking strength, tearing, opacity, porosity, double fold…
The Allimand double disk refiners exist in several sizes (20″, 28″ and 36″). They are Duoflo type refiners with two stock inlets allowing better refining balance and stability. These refiners are used for all sorts of application and especially for highly refined speciality papers.
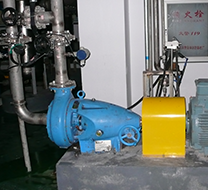
PULPING AND REFINING
DEFLAKING
Deflaking is an essential treatment not only for the disintegration of fibre bundles but also for ensuring a uniform stock consistency before refining or screening. Allimand has optimized this equipment thanks to its process and operational know-how. The company manufactures its own deflakers which are particularly adapted to virgin fibres and brokes, mainly for difficult papers like those resistant to water.
A deflaker is made up of:
- Resilient and abrasion resistant stainless steel rotor and stator fittings,
- Manual adjusting wheel with automatic positioning of the fittings,
- Mechanical and electrical safety devices,
- Dry stuffing boxes and or water ring.
STOCK PREPARATION
MIXING
The stability of the machine operation and the quality of the final fibre product results from the strict hydraulic and design rules. One of the key steps is mixing the various constituents of the stock. Allimand’s expertise excels in the homogeneous mixing of the different types of pulp (long fibre and short fibre), various additives and fillers. The direct process consequences are the constant retention of fibres and fillers and the natural tendency towards a quality formation.
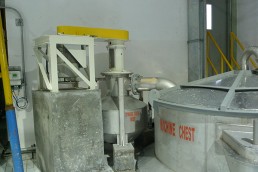
MIXING
DYNAMIC STOCK MIXER
The uniformity of the stock is essential for the stable running of the machine and the regularity of the paper characteristics in machine direction and cross direction.
Allimand has developed a revolutionary dynamic stock mixer which was first installed on speciality paper machine production lines and is now installed for all sorts of paper.
The various stock flows are injected in such a way that the mere injection enables a good mixture. A drilled plate and agitator finish the mixing of the different flows in a quick and constant manner.
This technology means that a mixing tank is no longer necessary. It also reduces the retention time and allows coloured paper to be changed quicker.
STOCK PREPARATION
APPROACH FLOW SYSTEM
The short circuit constitutes the final phase of the stock preparation before it is sent to the paper machine. Allimand has always been a leader in the design of this step, especially in terms of operation regularity (stock dilution control and automation of loops) and stock decontamination efficiency. This ensures an optimum and consistent supply of stock onto machine.
APPROACH FLOW SYSTEM
CLEANING
The cleanliness of the stock sent onto the machine is imperative in order to obtain a faultless paper, for example no fibre clusters, no black spots or holes. Allimand integrates a stock cleaning system into its approach flow systems. The design of each individual cleaner and the type of staging define the level of the cleaning efficiency and the limitation of fibre or filler loss. It ensures the elimination of light and heavyweight impurities and the air drawn in.
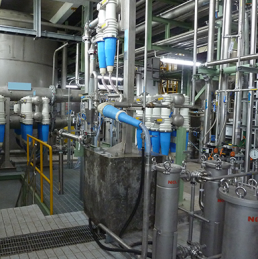
APPROACH FLOW SYSTEM
SCREENING
Screening with slotted holed baskets is the last treatment to the stock before it is sent to the paper machine. This process is essential for the cleanliness of the stock required for the production of paper without impurities. The presence of impurities can be the cause of paper breaks, an important factor in machine efficiency.
Screens are adapted depending on the fibre class and characteristics (wood, synthetic, natural). The number of stages is defined by the flows, residual fibre losses and the type of paper or fibre mat to be produced.
Allimand’s know-how and experience in the design of complex screening lines and in the production of hi-tech papers, guarantee the perfect adaptation of the systems with regards to operational constraints.
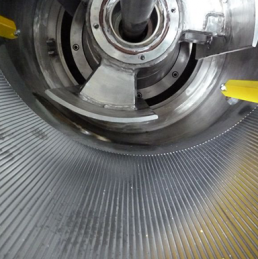
STOCK PREPARATION
BROKE SYSTEM
Recycling brokes in the stock preparation systems is always a critical step. Whether for wet or dry brokes, Allimand pays particular attention to the selection of pulp processing equipment according to the types of fibres, types of paper and the specific treatments made to the paper on the paper machine. Allimand’s expertise in this area, recognized around the world, is also the guarantee for an optimum consistency of the stock fed to the approach flow system.
BROKE SYSTEM
PULPING
The repulping of dry brokes is an important phase in pre slushing. It ensures the suspension of fibres and the dispersion of the biggest fibre clusters. The temperature and the duration of pulping together with the added specific additives prepare a refined and homogenous pulp ready for the following stages of treatment
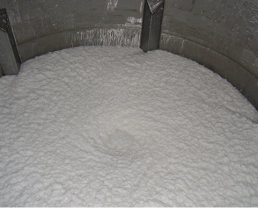
BROKE SYSTEM
DEFLAKING
The deflaker ensures the suspension of the dry brokes and is an important stage in pulp slushing. This process reduces the number of paper bundles by dividing the fibres and making them finer, particularly for water resistant papers. The pulp from the deflaker is then sent to a second stage of screening before being reintroduced into the brokes system.
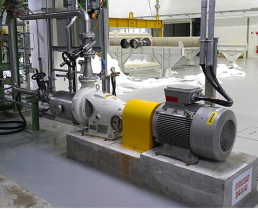
BROKE SYSTEM
SCREENING
The fibre suspension is directed towards the vibrating screen to separate the free fibres from the fibre bundles. This process eliminates contaminants which may have formed during the dry brokes treatment (stones, metal wires…). The contaminants are sent for a second deflaking treatment.
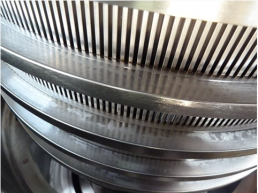
STOCK PREPARATION
WHITE WATER SYSTEM
The environmental constraints put on paper production sites (TSS, COD, fresh water consumption …) have determined the water recirculation process rules throughout the production plant. On the paper machine, the treatment of white water and its recycling once clarified have reduced all consumption and waste treatment ratios. Allimand’s knowledge and expertise are not limited to the choice of methods for best treating this water. They also concern the adequacy of the process with climatic conditions, the constraints of the kind of paper produced and the chemical consumption limits. Allimand’s experience in the market for high value-added papers means that for each type of fibre mat, a process will be chosen to ensure stable operating conditions of the paper machine.
WHITE WATER SYSTEM
WATER CLARIFICATION
Before clarification, the water can be pre filtered by a curved screen which eliminates felt hair from water coming from the press section. Water recycling is important for reducing the factory’s fresh water consumption. This simple and effective treatment ensures a more stable operation of the clarification system.
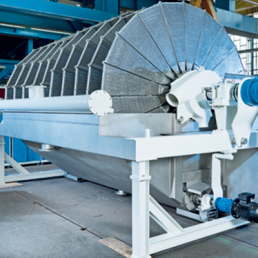
WHITE WATER SYSTEM
WHITE WATER TREATMENT
The surplus water from the white water systems are sent to a clarification treatment system. The three main methods used in the paper making industry are flotation, settling and filtration.
The choice of process depends on several parameters:
- Type of fibres (wood, natural, synthetic)
- Length of fibres
- Rate of fillers
- Physico-chemistry of the water
- Type of papers
- Specific process constraints
Allimand’s skill in the domain of water quality processes and its reuse is key for the production of quality, homogenous, faultless paper. The choice also affects the global fresh water consumption of the factory and the DOC and BOD values of the waste water.
The ever strict environmental constraints make this treatment a critical phase in the general process factory’s waste.
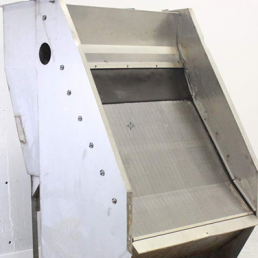