NEW SHOE PRESS PILOT
TECHNOLOGICAL DEVELOPMENT COMBINING ENERGY SAVING AND PERFORMANCE
ALLIMAND, designer and manufacturer of paper machines and paper industry equipment, continues its dynamic growth and develops its R&D skills by manufacturing a new shoe press pilot designed to optimize the performance of the paper sheet pressing and save energy. This new pilot named FAROS is installed on ALLIMAND’s industrial site in Rives (Isère, Rhône-Alps region) and its parts are also manufactured on an industrial scale.
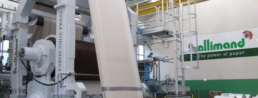
Green technology: “Produce more with less energy”
The shoe press technology keeps on expanding and taking a leading position for the manufacturing of continually varying paper types (packing paper, corrugated paper, cardboard paper…and so on).
Major advantages of this technology enable:
- To reach high dryness levels , while maintaining the paper sheet structure ; It is possible to enlarge its applications beyond packing papers for which this technology was previously limited.
- To save energy, on the paper sheet drying process as a result of the maximum pressing performance obtained with this technology.
A smart combination for an optimized operating performance
ALLIMAND is one of the very few paper machinery manufacturers to offer a single nip press section, hence called « Single Shoe Press». This pilot enables to use shoes with different shapes. It is fully equipped in order to control the drainage distribution between the upper and lower felts and which allows the optimization of the felt characteristics which is the main component for a successful shoe press installation.
A new technology designed to strengthen the credibility of our offer
“Our objective aims at offering our customers all-inclusive shoe press installations perfectly adapted to their products” says Simon CENA, ALLIMAND’s Managing Director. “With a leading position thanks to this technology, we will strengthen the credibility of our offer with our international customers.”
Technical data of the new Pilot:
- Maximum speed of 1800 m/mn
- Pressure of 1400 kN/m
- Possible to use shoes with different shapes.
- Fully equipped in order to control the drainage distribution between the upper and lower felts